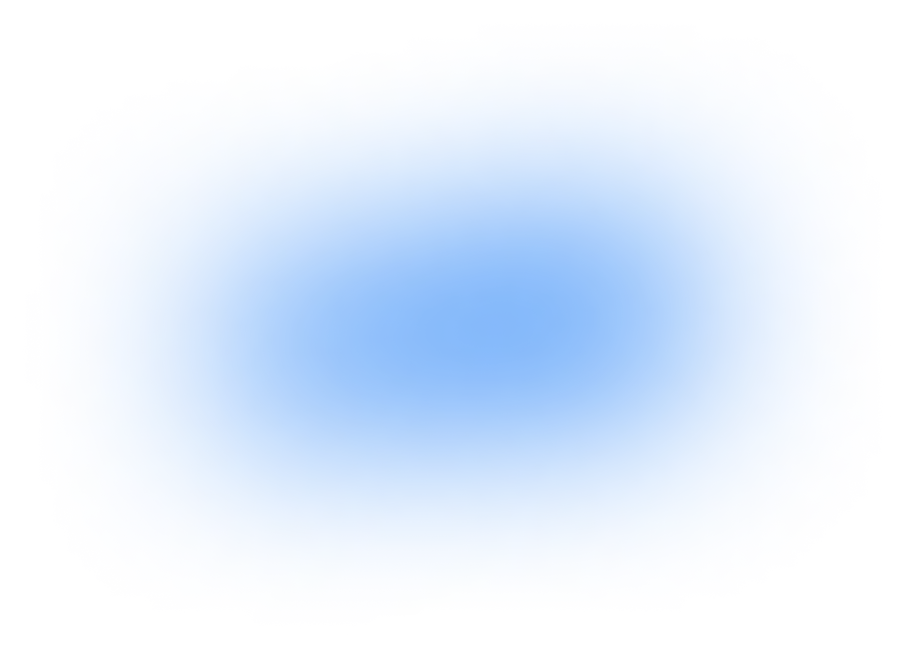

Case Study | SC Global Tubular Solutions
Transforming Tubular Goods Tracking
Automated and Transparent Supply Chain Management System
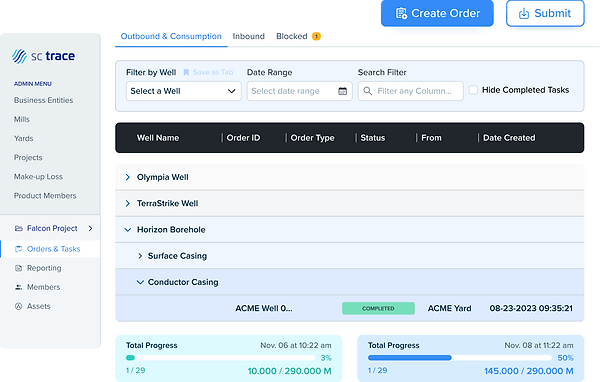
Overview
Umbrage partnered with Sumitomo Corporation Global Tubular Solutions (SCGTS) to develop a cutting-edge track and trace platform for tubular goods. This initiative aimed to automate and bring transparency to a traditionally paper-based industry.
Over 2.5 years, we collaborated to continually build and enhance SCGTS's digital product, providing a comprehensive solution to address expensive issues in monitoring drilling-related equipment, improving visibility of assets in the supply chain, and shortening payment cycles for operators.
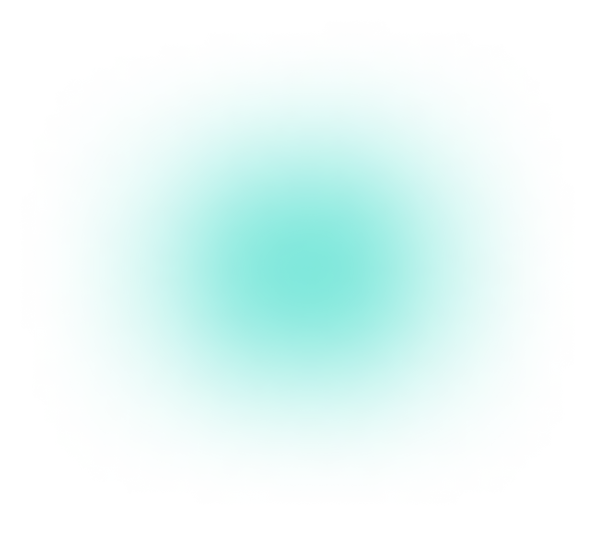
Our Approach
Supply Chain Optimization
Client Need
SCGTS, aimed to solve costly problems in tracking oil-related equipment, stock, and assets worldwide. These issues led to poor supply chain visibility and extended payment cycles for operators.
Product Definition
Learning from the Field
Umbrage and SCGTS conducted user interviews and site visits to understand field challenges that would allow the team to design a product tailored to real-world needs.
Product Development
High Standards
of Deployment
We focused on long-term product iterations, customer trials, and deployments, refining the solution through continuous feedback to meet high standards for
remote deployment.
Industrialization
Going the
Distance
Collaborating with SCGTS, we ensured the solution was deployable in remote areas with reliable off-line data syncing. The web and mobile apps replaced manual tallies, integrating seamlessly into yard and operations workflows.

The Results
Putting Power in the
Hands of the Field



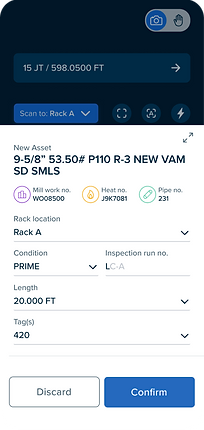

The Result
Features Overview
Umbrage delivered a scalable application that significantly improved visibility into the lifecycle of SCGTS's assets.
The platform was successfully implemented across global project sites, enhancing supply chain transparency and reducing tally times.
By eliminating antiquated paper processes, we modernized the supply chain, driving down operational costs and enabling faster and automated billing.
-
Global Deployment: Adaptive digital experience deployable globally, ensuring efficient and standardized workflows.
-
User Experience: Positive experience for both on-the-ground and back-office users.
-
Data Syncing: Reliable off-line data synchronization once devices are back on a network.
-
Scalability: Seamless scaling to accommodate growing user needs.
-
Automation: Automated billing and operational processes, reducing manual interventions.
-
Transparency: Improved visibility into asset lifecycle, enhancing decision-making and operational efficiency.